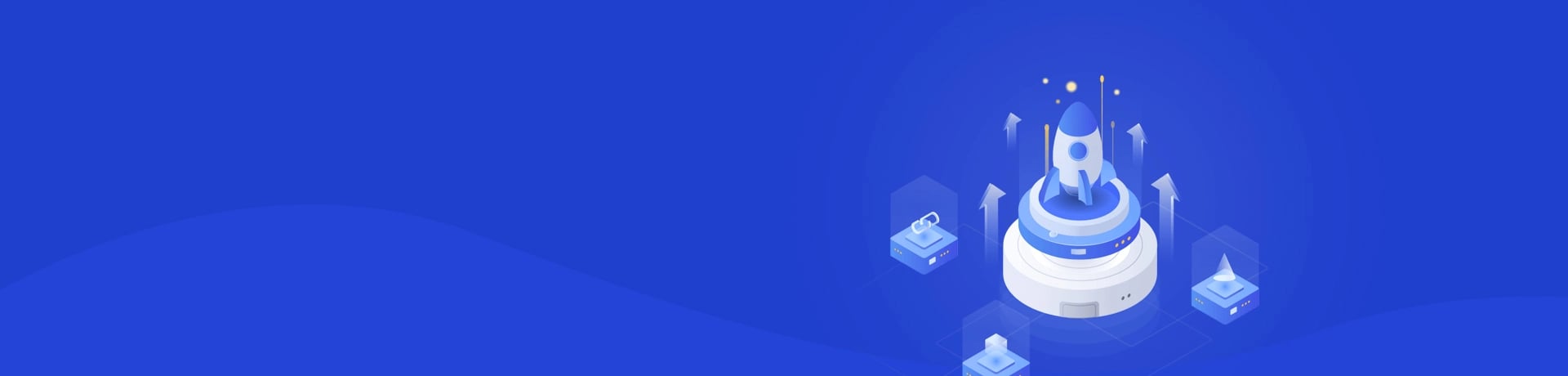
OrBit-MOM Platform
Not just an execution system, but an advanced management system
OrBit-EAM Enterprise Equipment Asset Management System
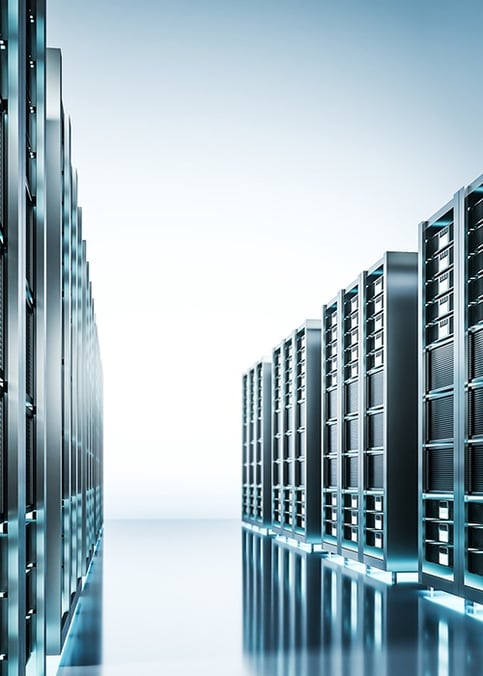
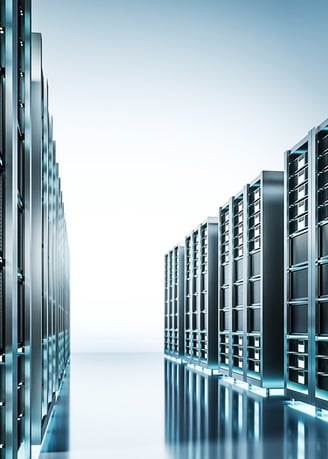
What Is OrBit-EAM System?
OrBit-EAM (Enterprise Asset Management), mainly includes: basic management, work order management, preventive maintenance management, asset management, operation plan management, safety management, inventory management, mobile asset barcode inventory, Basic functional modules such as procurement management, report management, maintenance management, and data collection management, as well as optional modules such as workflow management and electronic signage, to achieve:
Effectively understand the use of company assets
Reduce equipment failure rate and improve equipment reliability
Strengthen cost management and reduce overall maintenance and operating costs
Refine and standardize management to improve overall efficiency Improve effective OEE working time
Reduce equipment downtime Increase equipment usage efficiency
Relies on manual work, which is prone to omissions and management losses.
Equipment Asset Management Common Problem








Equipment repair costs, equipment failure, downtime losses and spare parts inventory costs remain high.
Equipment failures often occur, causing extremely serious losses.
Many idle items, confusing property rights, and unclear quantities.
There is great arbitrariness in purchasing.


Asset utilization is low and maintenance costs are high


System Function
BASIC INFORMATION MANAGEMENT
Provide warehouse location management to realize the association between warehouses and locations, and between locations and products.
INVENTORY INFORMATION MAINTENANCE
Manage the entire process of incoming and outgoing equipment and spare parts, integrate the warehouse management system, use real-time data to formulate inventory replenishment plans and reasonably arrange procurement base on lead times
SPARE PARTS MANAGEMENT
Provide basic data related to spare parts, inventory, procurement, warehousing and consumables part management by digitalization.
EQUIPMENT MAINTENANCE
Manage equipment repair reports, submit repair reports for review, assign technician, repair, approve results, and set important maintenance activities for different equipment for effectively prevent failures.
EQUIPMENT SCRAPPING TRANSFER
Manage equipment allocation and transfer, the system automatically calculates equipment depreciation information, and can dispose, scrap equipment base on cooperate need.
INVENTORY AUDIT
Initiate an inspection plan, allocate person in charge, support equipment photo uploading to effectively monitor equipment status. Equipment is connected online for inventory tracking, making the inventory process easy and convenient.
STATISTICAL ANALYSIS REPORT
The system automatically generates detailed data reports for equipment and spare parts. Statistics are simple and convenient, and can be displayed on web pages, APPs, electronic signboards, etc.
SYSTEM INTEGRATION
Supports integration with third-party systems such as ERP, MES and WES to achieve data interoperability and sharing to break information silos.
Product Core Advantage
01
Easy To Use
Has a easy understand user interface, built-in designer and smart workflow management.
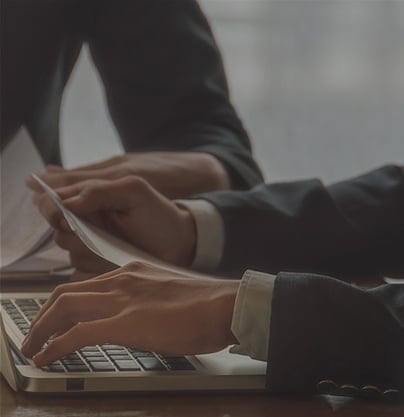
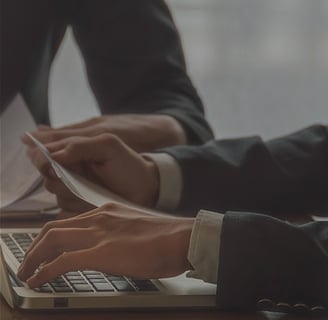
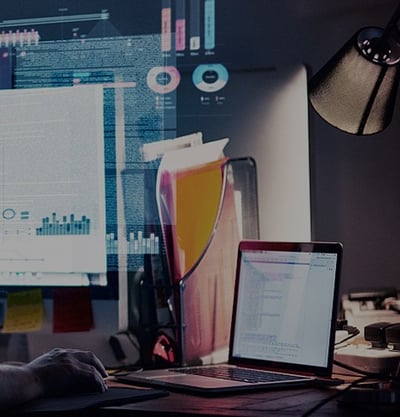
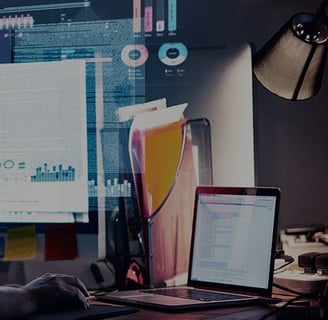
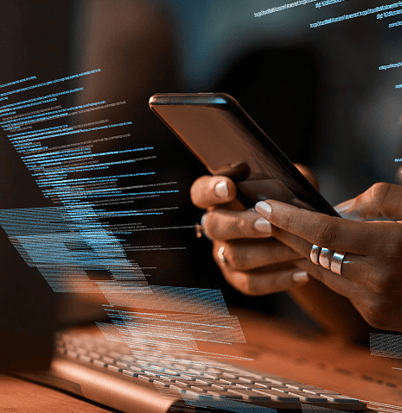
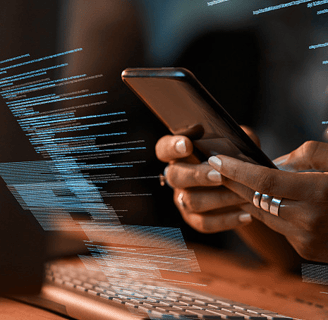
02
Custom Development
Supports flexible customized development according to needs, while open source supports enterprise secondary development.
03
Platform Integration
Supports system integration, with ERP MES,WMS and others systems.
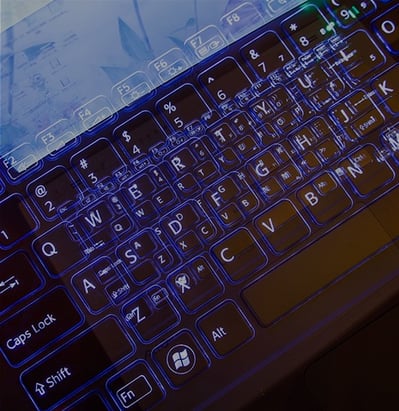
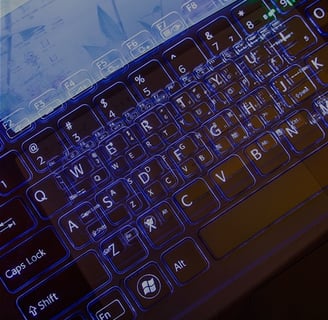
04
Safe And Reliable
Establish a complete security detection and monitoring mechanism to achieve the highest e-commerce level security
Bring Value to Enterprise
20 %
Improve Equipment Reliability
30%
25%
10%
Reduce Equipment Downtime
Extend Equipment Useful Life
70%
Improve Maintenance Efficiency
Reduce Inventory Costs
© 2024. ALL RIGHT RESERVED HUALEI SOLUTIONS SDN. BHD. 202401027873(1573722-T)