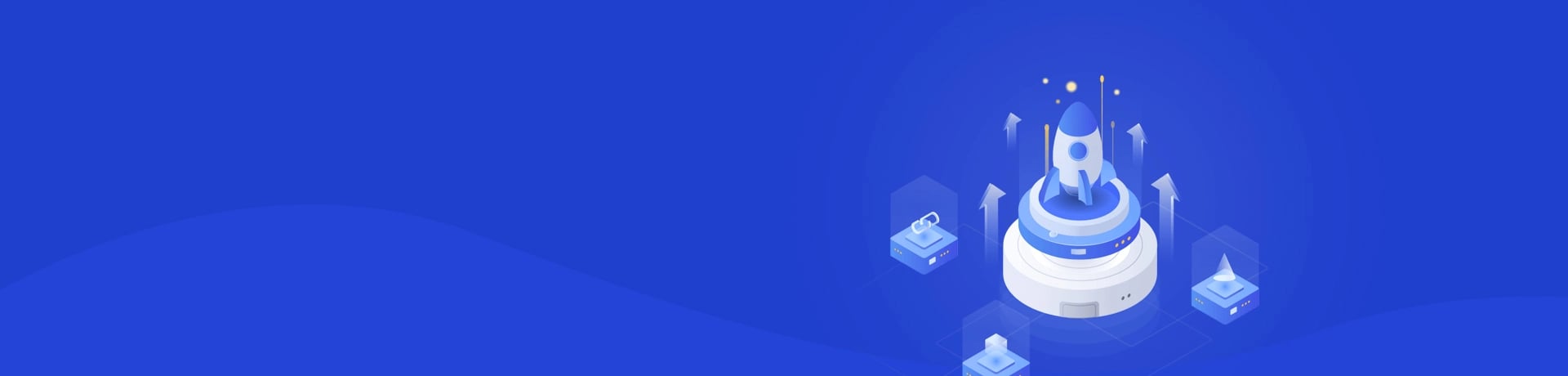
OrBit-MOM Platform
Not just an execution system, but an advanced management system
OrBit-SCADA Supervisory Control and Data Acquisition
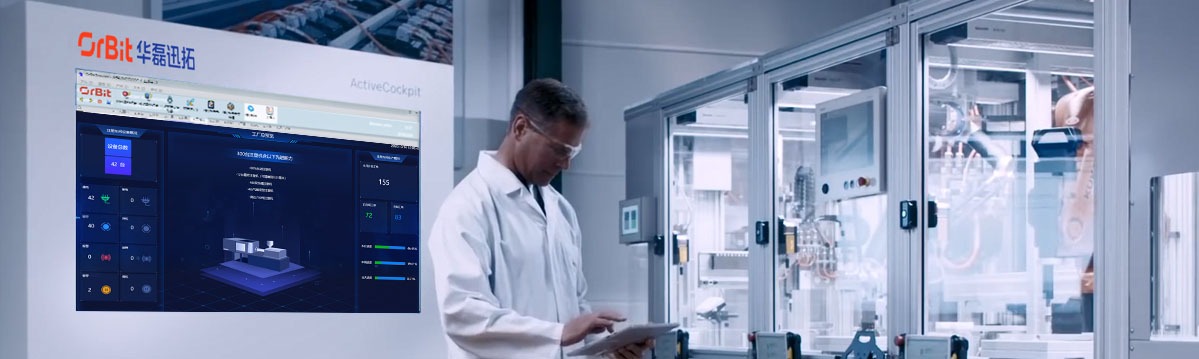
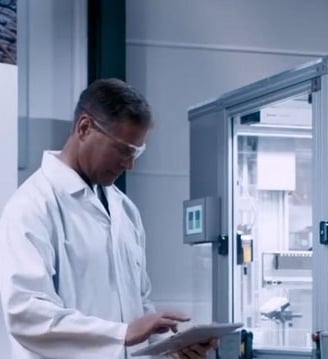
What Is OrBit-SCADA System?
The OrBit-SCADA (Supervisory Control And Data Acquisition) system is the specific implementation of the "Manufacturing Internet of Things Information". It contains two important level: First, remote real-time data acquisition system, which a industrial communication and control with server system; then is the scene modeling and display system at the production site
OrBit-SCADA uses industrial communication protocols such as OPC/Modbus/SECS to connect various intelligent controller in the factory. These connected controller are equip with production process and transaction management equipment or instruments to sense the status of various process parameters of the equipment, convert these status signals into digital signals, and transmit them to OrBit-SCADA through a specific digital communication network. When necessary, OrBit-SCADA can also send control signals to the controller. After receiving the feedback information from the controller, OrBit-SCADA displays it to user in appropriate forms such as sounds, graphics, images, etc., to achieve the purpose of monitoring. After the data is processed, it informs the user of the status of various parameters of the device (alarm, Normal or alarm recovery), these processed data may be screened and saved in the database of the OrBit-MES manufacturing execution system, or they may be transmitted to different monitoring platforms through the network system.
Based on HTML5 WebSCADA Configuration System
OrBit-WebSCADA system is a new generation of SCADA where presentation layer is based on pure HTML5 and WebSocket technology. It is mainly used for cross-platform real-time device configuration. It can support Android/iOS browsers, has powerful functions and performance. Easy to deploy and rich in display effects. At the same time, it also has a powerful web visual designer and runtime.
OrBit-SCADA Technical Specification
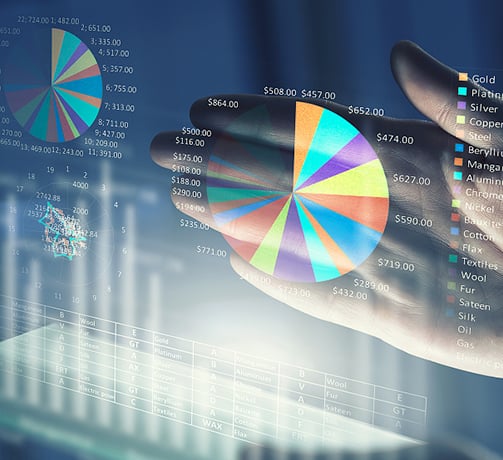

Visual scene configuration modeling
Based on Microsoft .Net and WPF technology
Embedded C#.Net and Javascript script engine
More than 3,000 built-in galleries
Support email, SMS alarm
Support Sqlite, SQLServer, ODBC database
Support customized startup screen and help information
Event replay and trend analysis
Support OPC/ModBUS/SECS-GEM/RS232/Socket protocol
Supports 32-bit and 64-bit Windows systems
Built-in micro OPC server supports XML data exchange
Completely integrated with OrBit-X/OrBit-MES
Feature And Advantage
01
Monitoring Of Process Parameters And Equipment Status
Graphically display the factory's production process, and link machine indicators and display them in real time. The interface drawing takes into account the overall process flow, and the data points are closely related to the interface. The interface adopts a modular design to facilitate the user's visual experience. The overall interface adds equipment visualization processing elements to achieve the effect of knowing by looking at the picture; The pipeline-based detailed design data flow further demonstrates the process execution process.
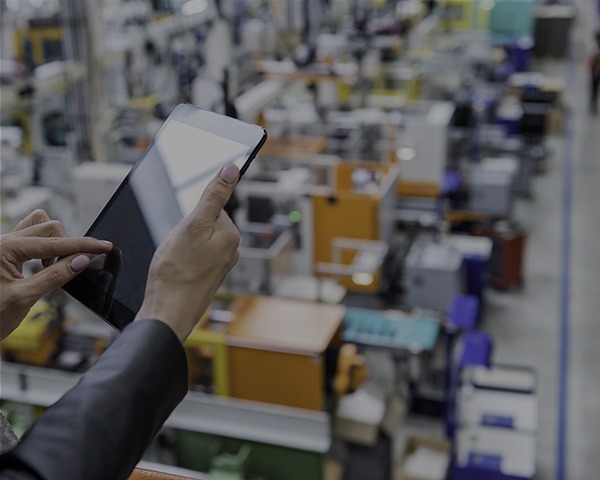
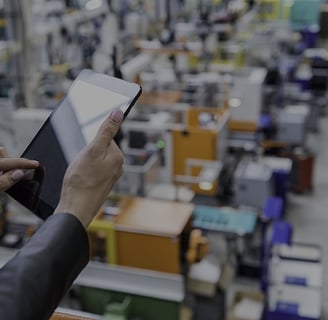
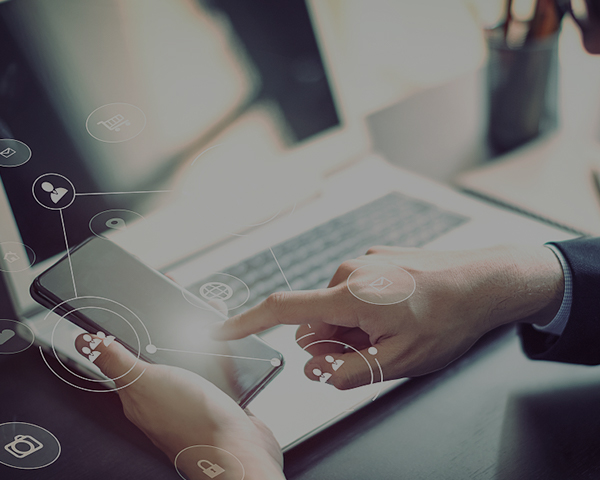
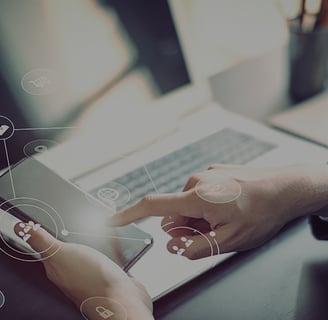
02
Real-Time Data Analysis, Archiving, Trend Display
The system records the history of each data point, and the recording frequency reaches the second level. User can specify time frame to retrieve process data, form data tables and curve trends to help users better analyze the stability of the indicators and whether there are abnormalities. Historical data points are closely related to the machine, and the corresponding process indicators can be retrieved through the machine.
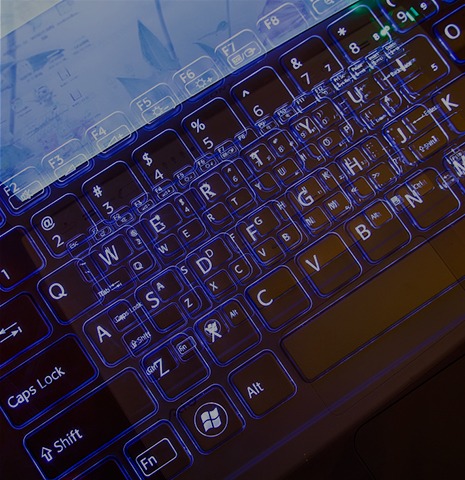
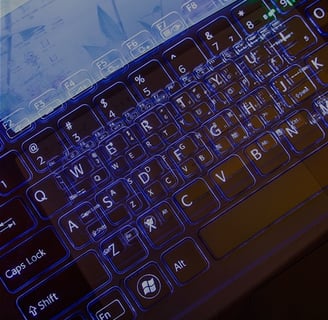
03
Alarm, Warning
Real-time monitoring of whether various process parameter meet the process requirements, timely alarms for indicators that do not meet the process range, and highlighting in the interface through colors. The function of saving and query abnormal information records has been added. For the alarm threshold, manual modification function is provided, which can be adjusted according to the actual operating conditions.
Why Choose US?
24 Years
Professional Service Team
Industry Leading Customers
200+
800+
100%
Deep Cultivation In The Industry
Project Implementation
© 2024. ALL RIGHT RESERVED HUALEI SOLUTIONS SDN. BHD. 202401027873(1573722-T)