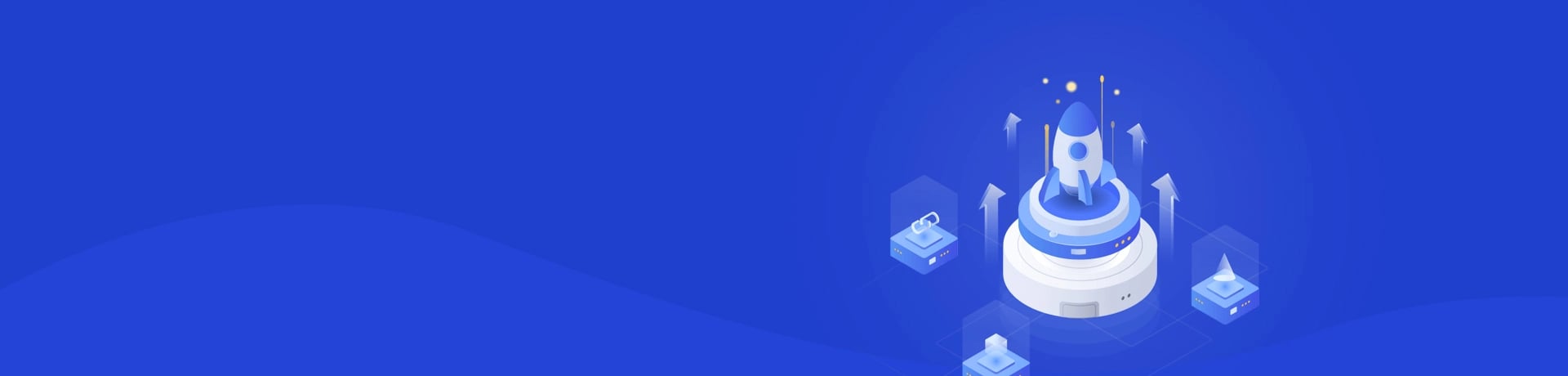
OrBit-MOM Platform
Not just an execution system, but an advanced management system
OrBit-RCS Remote Centralized Control System
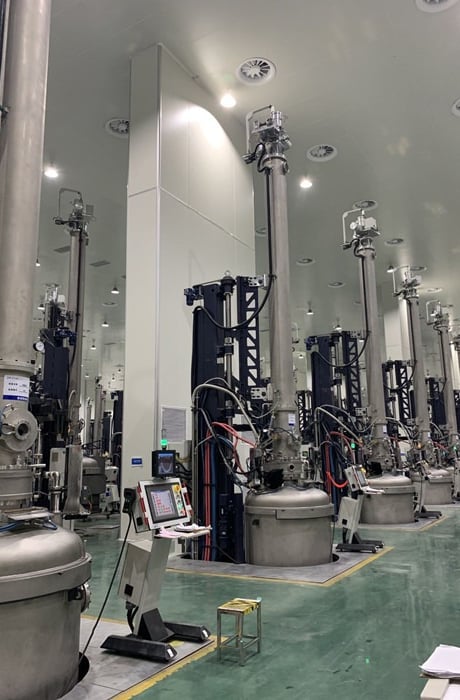
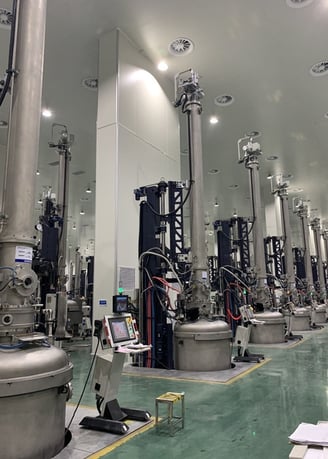
What Is OrBit-RCS System?
OrBit-RCS is "OrBit Remote Control System". It is mainly target to PC base terminal equipment application scenarios for industrial in electronic materials, photovoltaics, LEDs, semiconductors, components, etc. It designed for remote connection of any PC terminal base equipment. Get the current operation screen video streams of multiple PC terminals in real time and then send remote mouse and keyboard messages to remotely controlled PC terminal in real time. On the remote centralized control computer, you can quickly control the real-time dynamically of each industrial pc terminal and make corresponding operations.
The advantages of the OrBit-RCS system are: reducing staff and increasing efficiency, fast processing, real-time control, and reducing the time cost for person in charge entering the manufacturing floor. The system will generate huge economic benefits for the enterprise when combined with the OrBit-SCADA and OrBit-KANBAN systems. It is an IT The most intuitive result of integrating with OT.
A large number of professionals operate equipment:
The threshold for operating equipment has increased, and professionals need to be recruited to operate the equipment;
The scale of the factory has increased, the factory area has increased, and the number of people has increased;
The number of professionals has increased, making it difficult to reduce labor costs;
Professional employee substitutability is poor and risks in production and operation activities increase
Management Of High Density Equipment Production Floor






Difficulties in ensuring process consistency:
Manual synchronization of process file versions for stand-alone equipment, resulting in poor consistency;
Use of mobile storage media to deliver process files to equipment, making it difficult to prevent viruses;
Process parameter update steps are cumbersome and severely fragmented;
The lag in process control results in low product production performance and production capacity.
Difficulties in unified management of equipment:
1. The equipment is distributed in a large area, making it difficult to comprehensively and quickly grasp the operating status of the equipment;
2. Alarm information is scattered, making it difficult to detect and process in time, causing losses;
3. The equipment is scattered, making inspection difficult, and it is difficult to detect hidden risk ;
4. It is difficult to replace shift equipment operators in different sections.
OrBit-RCS System Application Scenarios
Man Power Efficiency
Scenario 1: After a single crystal production factory implemented RCS, the original 6 skilled workers lead six interns to operate 48 sets of single crystal growth equipment per-shift, change to one skilled worker lead one intern to operate 48 pieces of equipment. And there is still room for improvement to greatly reduce reliance on professionals.
The RCS system can effectively improve man power efficiency and reduce dependence on professionals.
Centralized control of equipment to reduce the number of inspection personnel.
Small number of professionals lead some newcomers to execute production activities.
Total number of equipment operators is reduced.
Technology Protection
Scenario 2: Before the implementation of RCS in a workshop, process files was transfer to Equipment PC using USB storage and the virus was infected and spread in the workshop through the equipment network, causing production losses. After the implementation of RCS, the process files are automatically synchronized by the server, which is real-time, accurate and safe, ensuring production safety.
The RCS system supports the unified issuance of process documents to ensure consistency in process execution.
The centralized control center issues process documents uniformly to ensure uniformity.
Simplify the delivery process and eliminate the need for mobile storage media testing.
Eliminate foreign viruses and ensure the system security of production equipment.
Equipment Inspecting
Scenario 3: Before the implementation of RCS in a workshop, one inspection man power was arranged to perform equipment inspections 12 units of equipment, and the efficiency was low. After implementation of RCS, the video and parameter inspection work was performed by the equipment operator. Directly eliminate the need for inspection man power.
The RCS system effectively improves equipment inspection efficiency
The centralized control system has equipment video, parameter transmission, and centralized control terminal inspection capabilities.
Equipment alarms are uniformly displayed and reminded in the centralized control area .
Centralized control operators can inspect and handle equipment problems without arrive at machine site.
Equipment Management
Scenario 4: After a factory implemented a RCS for different sections of the factory for a period of time, it realized inspections and control of the factory's main equipment in the centralized control room. Through rotation training, it built the ability to rotate centralized control workers in different sections.
The RCS system effectively improves the integrated management of equipment
Theoretically, any equipment that can be operated with mouse keys can be used for centralized control system construction.
The centralized control system breaks the time and space constraints of equipment operation.
The centralized control system models the operator operating equipment into several category including inspection, alarm handling and remote control from centralized control room. This reduces the difficulty for centralized control operators to change position across work sections.
Benefits Of Implementing The OrBit-RCS System
01
Operation Efficiency
Centralized and real-time control of equipment, real-time push of alarm information, shortening the response time toward equipment failures and anomalies and improving reliability. At the same time, it reduces the ineffective actions of personnel at the production site to inspecting process parameters and modifying equipment setting.
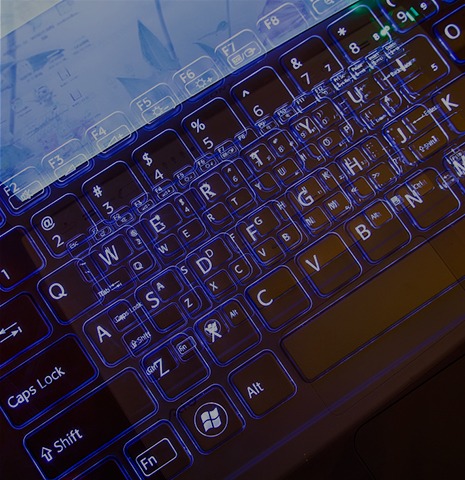
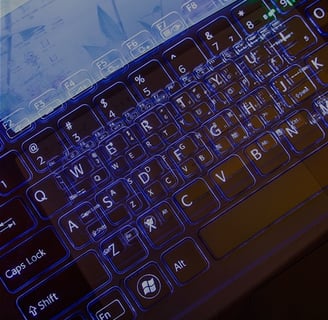
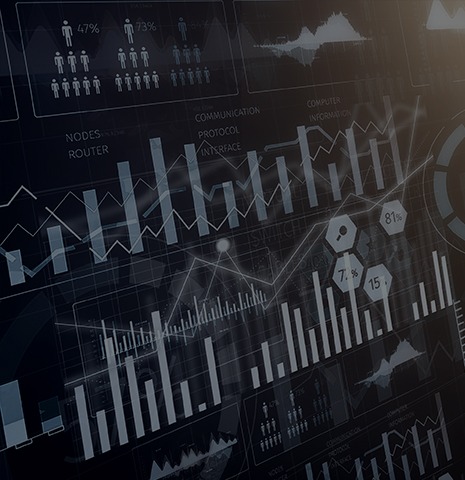

02
Parameter Monitoring
Abnormalities and alarms can be discovered quickly, accurately and processed in a timely manner to improves. Process parameters are monitored and distributed centrally, reflecting standardization and neatness, enhancing quality assurance compliance, and improving corporate competitiveness strength.
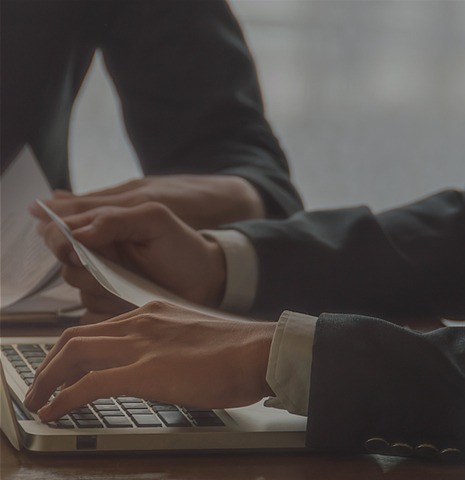
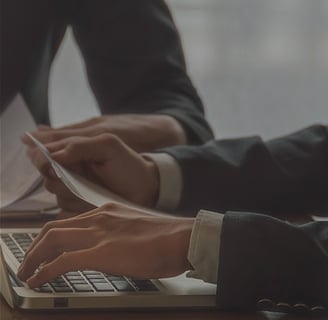
04
Alarm, Warning
Count the life span and maintenance intervals of equipment and mold fixtures based on factors such as output and machine operation time, provide early warning, alarm, and shutdown services, and urge the equipment operation and maintenance department to carry out maintenance work as planned. Indirectly improving quality and ensuring the continuity of equipment availablility.
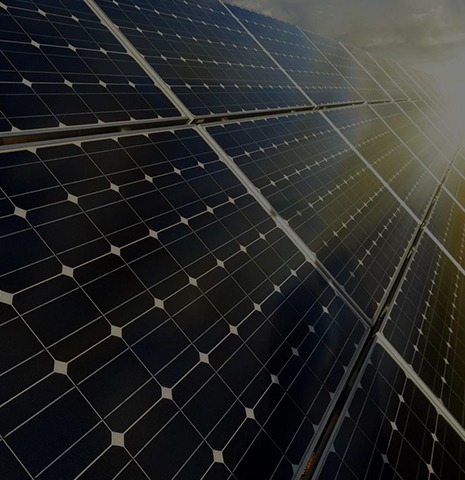
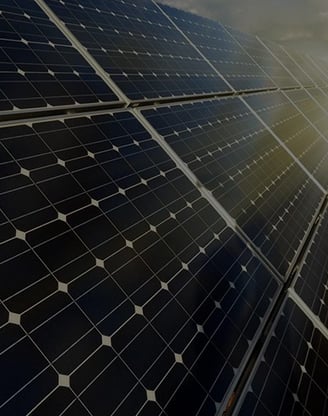
03
Real Time Status
Automatically record equipment operators logging in/out of the equipment, establish assessment files, and control equipment operations; centralized monitoring makes information and status real-time and transparent, shortening the information distance between the production line and the management room.
© 2024. ALL RIGHT RESERVED HUALEI SOLUTIONS SDN. BHD. 202401027873(1573722-T)