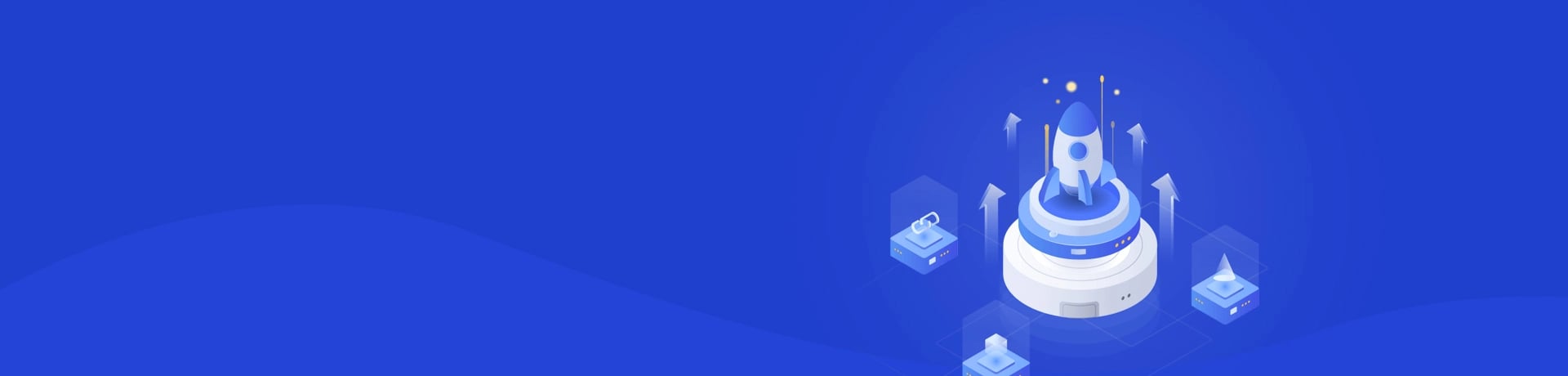
OrBit-MOM Platform
Not just an execution system, but an advanced management system
OrBit-WMS Warehouse Management System
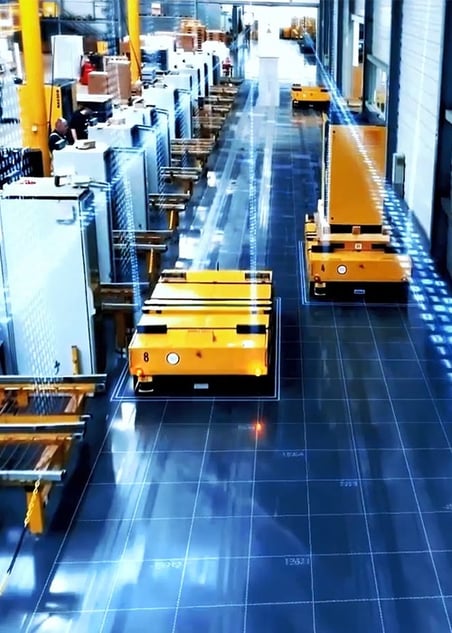
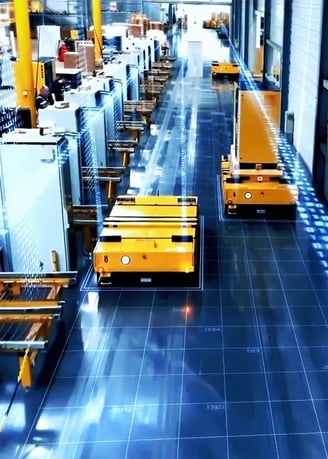
What Is OrBit-WMS System?
OrBit-MES system is a Warehouse Management System. It manages batches through functions such as warehousing business, outbound business, warehouse allocation, inventory allocation and virtual warehouse management. A management system that comprehensively uses functions such as management, material correspondence, inventory counting, quality inspection management, virtual warehouse management, and real-time inventory management to effectively control and track the entire logistics and cost management process of warehouse business, and realize or improve enterprise warehousing information management.
Supply chain management is chaotic: different barcodes, confusing coding standards, and difficult management.
Warehouse Management Common Problem










Low operating efficiency: difficult to find materials, and return materials.
Low accuracy: It is easy to make mistakes when entering and exiting the warehouse, and the inventory accuracy is not high.
Difficulty in batch management : first-in-first-out is difficult to implement, and there are many sluggish products.
Difficulty in manpower management: it is difficult for new employees to get familiar with system, performance management is difficult, and labor costs are high.


Difficulty in inter-departmental collaboration: data is not timely and inconsistent, and reconciliation is difficult.


Chaotic on-site management: irregular processes, low floor area ratio, and large waste of space.
Black hole of online warehouse management: unclear inventory, no matter what area.


OrBit-WMS System Core Functions
LOCATION MANAGEMENT
Provide warehouse location management to realize the association between warehouses and locations, and between locations and products.
WAREHOUSING MANAGEMENT
Quickly generate barcode labels and automatically prompt for shelf locations.
WAREHOUSE MANAGEMENT
Supports multiple picking strategies to achieve the shortest picking path
MATERIAL QUALITY INSPECTION
Connect with IQC inspection equipment to automatically obtain IQC test results.
REPLENISHMENT MANAGEMENT
Automatically remind replenishment based on inventory warning, support emergency manual replenishment and reduce picking waiting time.
STOCK OFF THE SHELF
Provide a complete set of inspections for material preparation and provide a material preparation list based on first-in, first-out
BARCODE MANAGEMENT
Full barcode management, supporting barcodes, QR codes, RFID, and electronic labels.
AGV INTEGRATION
By integrating and dispatching AGVs, we can realize unmanned movement of goods and improve the efficiency of warehousing operations.
KANBAN MANAGEMENT
Real-time display of personnel performance, document picking progress, abnormal situations, etc.
INVENTORY MANAGEMENT
Automatically generate various reports for the warehouse and present them in a digital format to facilitate inventory status.
Product Core Advantage
01
Flexible Configuration
Provides warehouse business process modeling functions and flexible business process configuration
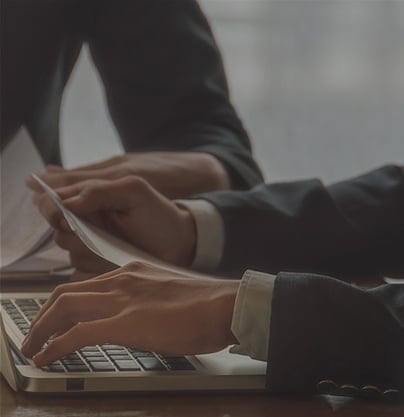
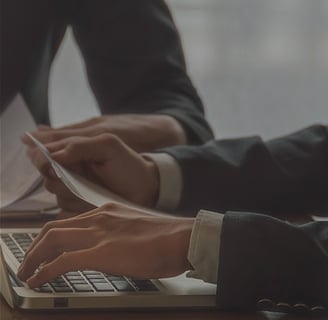
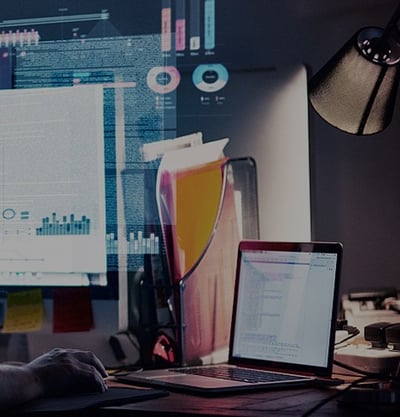
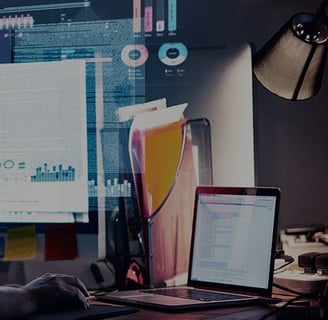
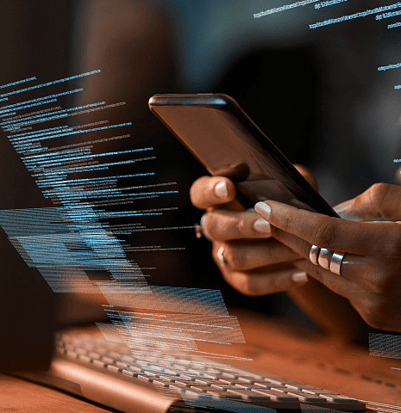
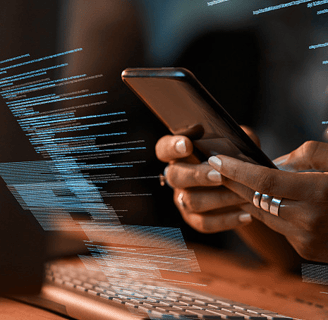
02
Mobile Work
Use handheld device terminals to realize mobile operations through wireless communication technology
03
Platform Integration
Supports system integration, with ERP MES and others systems.
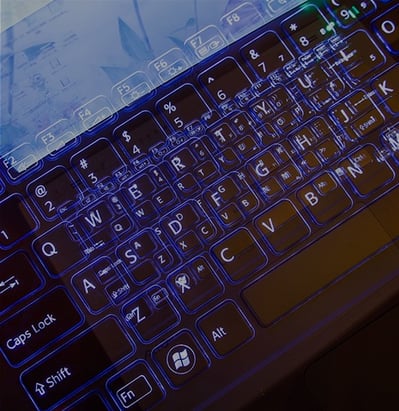
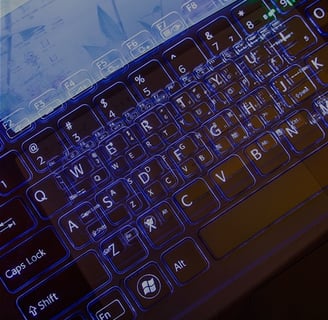
04
Standard Barcode
Establish a standardized system, use barcode operations throughout the process, to achieve paperless operation.
Bring Application Value To Enterprises
20%
Reduce Management Cost
Reduce Late Delivery Losses
20%
20%
100%
Reduce Inventory
Achieve Accuracy
80%
Reduce Slow Moving Inventory
40%
Reduce Time To Locate Inventory
30%
Improve Information Transparency And Validity
30%
Reduce Manual Operation Time
© 2024. ALL RIGHT RESERVED HUALEI SOLUTIONS SDN. BHD. 202401027873(1573722-T)